In today’s rapidly evolving technological landscape, the importance of advanced electronic cable assembly cannot be overstated. While often overlooked, these intricate networks of wires, connectors, and assemblies form the nervous system of our modern electronic world. From satellites orbiting the Earth to the robots working alongside humans in factories, high-quality custom wiring harnesses and cables play a crucial role in ensuring the reliability, efficiency, and performance of complex electronic systems.
This article explores the significance of advanced electronic cable assembly across various industries and applications, highlighting how these components are meeting the world’s ever-changing needs in sectors such as satellites, interior lighting, automation equipment, robotics, and custom cable solutions.
High-Quality Custom Wiring Harnesses and Cables
At the heart of advanced electronic cable assembly are custom wiring harnesses and cables. These are not off-the-shelf components but rather bespoke solutions designed to meet the specific requirements of each application. The benefits of custom wiring harnesses include:
- Optimized Performance: Tailored to the exact specifications of the system, custom harnesses ensure optimal signal integrity and power delivery.
- Space Efficiency: In applications where space is at a premium, such as satellites or compact robots, custom harnesses can be designed to fit precisely within the available space.
- Weight Reduction: Especially critical in aerospace applications, custom harnesses can be optimized to minimize weight without compromising functionality.
- Environmental Resistance: Custom cables can be designed with specific materials and shielding to withstand harsh environments, from the vacuum of space to the corrosive atmospheres in industrial settings.
- Simplified Installation and Maintenance: Well-designed custom harnesses can significantly reduce installation time and simplify future maintenance or upgrades.
In today’s rapidly evolving technological landscape, the importance of advanced electronic cable assembly cannot be overstated. While often overlooked, these intricate networks of wires, connectors, and assemblies form the nervous system of our modern electronic world. From satellites orbiting the Earth to the robots working alongside humans in factories, high-quality custom wiring harnesses and cables play a crucial role in ensuring the reliability, efficiency, and performance of complex electronic systems.
This article explores the significance of advanced electronic cable assembly across various industries and applications, highlighting how these components are meeting the world’s ever-changing needs in sectors such as satellites, interior lighting, automation equipment, robotics, and custom cable solutions.
High-Quality Custom Wiring Harnesses and Cables
At the heart of advanced electronic cable assembly are custom wiring harnesses and cables. These are not off-the-shelf components but rather bespoke solutions designed to meet the specific requirements of each application. The benefits of custom wiring harnesses include:
- Optimized Performance: Tailored to the exact specifications of the system, custom harnesses ensure optimal signal integrity and power delivery.
- Space Efficiency: In applications where space is at a premium, such as satellites or compact robots, custom harnesses can be designed to fit precisely within the available space.
- Weight Reduction: Especially critical in aerospace applications, custom harnesses can be optimized to minimize weight without compromising functionality.
- Environmental Resistance: Custom cables can be designed with specific materials and shielding to withstand harsh environments, from the vacuum of space to the corrosive atmospheres in industrial settings.
- Simplified Installation and Maintenance: Well-designed custom harnesses can significantly reduce installation time and simplify future maintenance or upgrades.
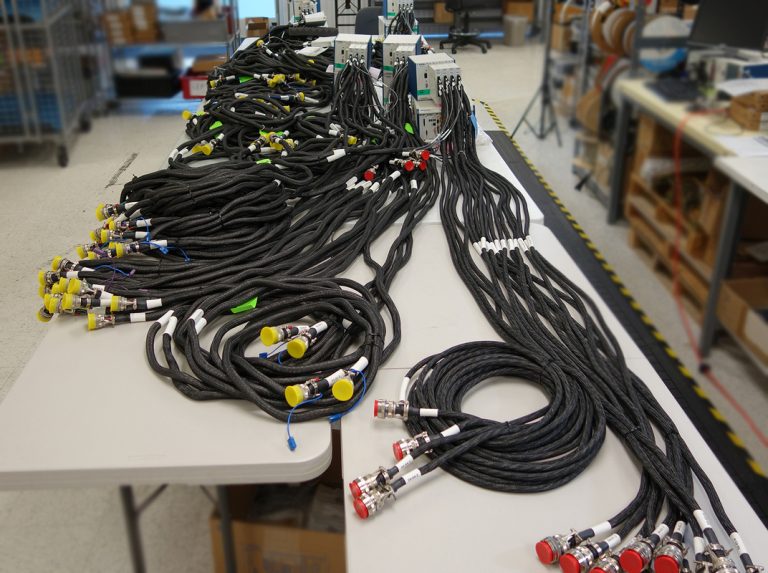
Connectors: The Critical Junction Points
Connectors are the unsung heroes of electronic systems, providing reliable interfaces between different components. Advanced connector technologies are pushing the boundaries of what’s possible in electronic design:
1. High-Speed Data Transmission: Modern connectors support ever-increasing data rates, crucial for applications like 5G networks and high-performance computing.
2. Miniaturization: As devices shrink, so do connectors. Micro and nano connectors allow for high-density connections in compact devices.
3. Ruggedized Designs: Connectors for industrial and military applications are built to withstand extreme conditions, including high vibration, temperature extremes, and exposure to chemicals.
4. Quick-Connect Systems: In applications where rapid assembly or field-serviceability is important, quick-connect systems allow for fast and reliable connections without specialized tools.
5. Hybrid Connectors: These advanced connectors combine power, signal, and even fluid or gas connections in a single interface, streamlining system design.
Electromechanical and Box Builds
Beyond cables and connectors, many modern electronic systems require complete electromechanical assemblies or box builds. These integrated solutions offer several advantages:
1. Simplified Supply Chain: By sourcing a complete assembly from a single supplier, manufacturers can reduce complexity and potential points of failure.
2. Quality Control: Integrated assemblies can be thoroughly tested as a unit before installation, ensuring compatibility and performance.
3. Customization: Box builds can be tailored to specific form factors and environmental requirements, perfect for unique applications.
4. Reduced Time-to-Market: Pre-assembled and tested units can significantly speed up product development and deployment cycles.
5. Scalability: As production needs change, working with a supplier on complete assemblies can provide more flexibility than managing multiple component suppliers.
Electromechanical and Box Builds
Beyond cables and connectors, many modern electronic systems require complete electromechanical assemblies or box builds. These integrated solutions offer several advantages:
1. Simplified Supply Chain: By sourcing a complete assembly from a single supplier, manufacturers can reduce complexity and potential points of failure.
2. Quality Control: Integrated assemblies can be thoroughly tested as a unit before installation, ensuring compatibility and performance.
3. Customization: Box builds can be tailored to specific form factors and environmental requirements, perfect for unique applications.
4. Reduced Time-to-Market: Pre-assembled and tested units can significantly speed up product development and deployment cycles.
5. Scalability: As production needs change, working with a supplier on complete assemblies can provide more flexibility than managing multiple component suppliers.
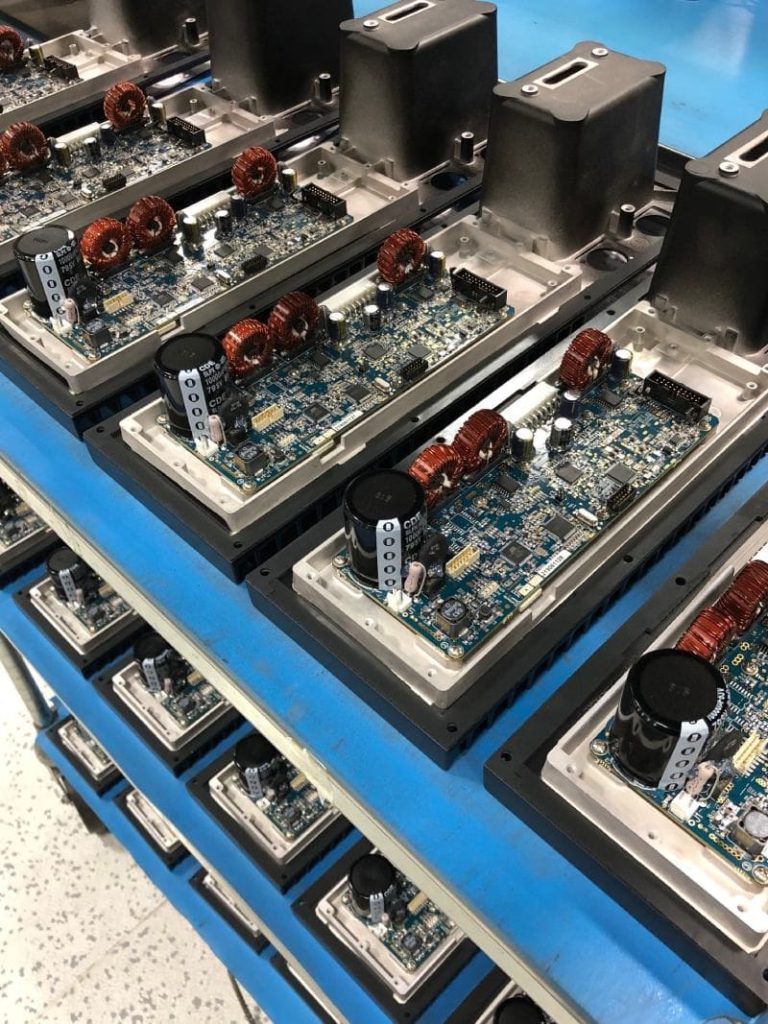
Industry Applications
Satellites:
In the demanding realm of space technology, advanced cable assemblies are mission-critical. Satellite systems require ultra-reliable, lightweight, and radiation-resistant cable solutions. Custom harnesses for satellites must withstand extreme temperature fluctuations, vacuum conditions, and high levels of electromagnetic interference. The ability to transmit high-frequency signals with minimal loss is crucial for communication satellites, while power distribution harnesses must be incredibly efficient to make the most of limited onboard energy resources.
Interior Lighting:
Modern interior lighting systems, especially in commercial and high-end residential applications, rely heavily on advanced cable assemblies. These systems often integrate complex controls, sensors, and networking capabilities. Custom wiring harnesses enable seamless integration of LED fixtures, dimming controls, occupancy sensors, and smart home systems. In architectural lighting, where aesthetics are paramount, ultra-thin and flexible cable assemblies allow for creative lighting designs without visible wiring.
Automation Equipment:
The fourth industrial revolution, or Industry 4.0, is driven by automation equipment that depends on sophisticated cable assemblies. These systems require high-speed data transmission for real-time monitoring and control, often in environments with significant electromagnetic interference. Custom cable assemblies in automation equipment must often combine power delivery, data transmission, and sometimes pneumatic or hydraulic lines in a single, easy-to-install package. Durability is key, as these assemblies must withstand constant motion, vibration, and potential exposure to oils and chemicals.
Robotics:
In the fast-evolving field of robotics, cable assemblies face unique challenges. Robots require cables that can withstand repeated flexing and torsion without failing. For collaborative robots working alongside humans, cable assemblies must be designed with safety in mind, often incorporating features like quick-disconnect systems for emergency situations. In more specialized applications like surgical robots, cable assemblies must be sterilizable and incredibly precise to enable delicate operations.
Custom Cables:
The realm of custom cables extends far beyond these specific industries. From medical devices requiring biocompatible materials to underwater remotely operated vehicles (ROVs) needing pressure-resistant cables, the possibilities are endless. Custom cable solutions are also crucial in emerging technologies like electric vehicles, where high-voltage power distribution and complex sensor networks demand innovative cable designs.
Conclusion
As we’ve seen, advanced electronic cable assembly plays a pivotal role in enabling the sophisticated electronic systems that power our modern world. From the heights of space to the depths of the ocean, from sprawling factories to the lighting in our homes, custom wiring harnesses, connectors, and electromechanical assemblies are the unsung heroes of technological progress.
As technology continues to evolve at a breakneck pace, the demands placed on electronic cable assemblies will only increase. Higher data rates, more extreme environments, and ever-shrinking form factors will drive innovation in materials, design techniques, and manufacturing processes.
For companies developing cutting-edge electronic systems, partnering with experienced cable assembly specialists is more crucial than ever. The right cable assembly solution can be the difference between a good product and a great one, between meeting specifications and exceeding them.
In our interconnected world, it’s the connections themselves – the wires, cables, and connectors – that often determine the limits of what’s possible. As we look to the future, advanced electronic cable assembly will continue to push those limits, enabling the next generation of technological marvels that will shape our world.