The relentless march of technology continues to drive the demand for smaller, lighter, more powerful, and increasingly, flexible electronic devices. Wearable technology, from smartwatches and fitness trackers to advanced health monitoring systems, is rapidly expanding. Simultaneously, the medical device industry is pushing the boundaries of miniaturization and minimally invasive procedures. These trends are placing unprecedented demands on electronic components, and traditional rigid printed circuit boards (PCBs) are often unable to meet the challenges.
This is where flexible and rigid-flex PCBs become essential. These innovative circuit board technologies are enabling the next generation of wearable and medical devices, offering unprecedented design flexibility, reduced size and weight, and enhanced reliability. BENCOR, a leading provider of PCB design, manufacturing, and assembly services, is at the forefront of this technological revolution, providing cutting-edge solutions for these demanding applications.
What are Flexible and Rigid-Flex PCBs?
To understand the transformative potential of these technologies, it’s crucial to define the terms:
Flexible PCBs (Flex Circuits): These circuits are built on a flexible substrate material, typically polyimide (e.g., Kapton), which allows them to bend, twist, and conform to various shapes. They consist of conductive traces (usually copper) etched onto the flexible substrate and often covered with a protective layer (coverlay). The key characteristic is their ability to flex without breaking the electrical connections.
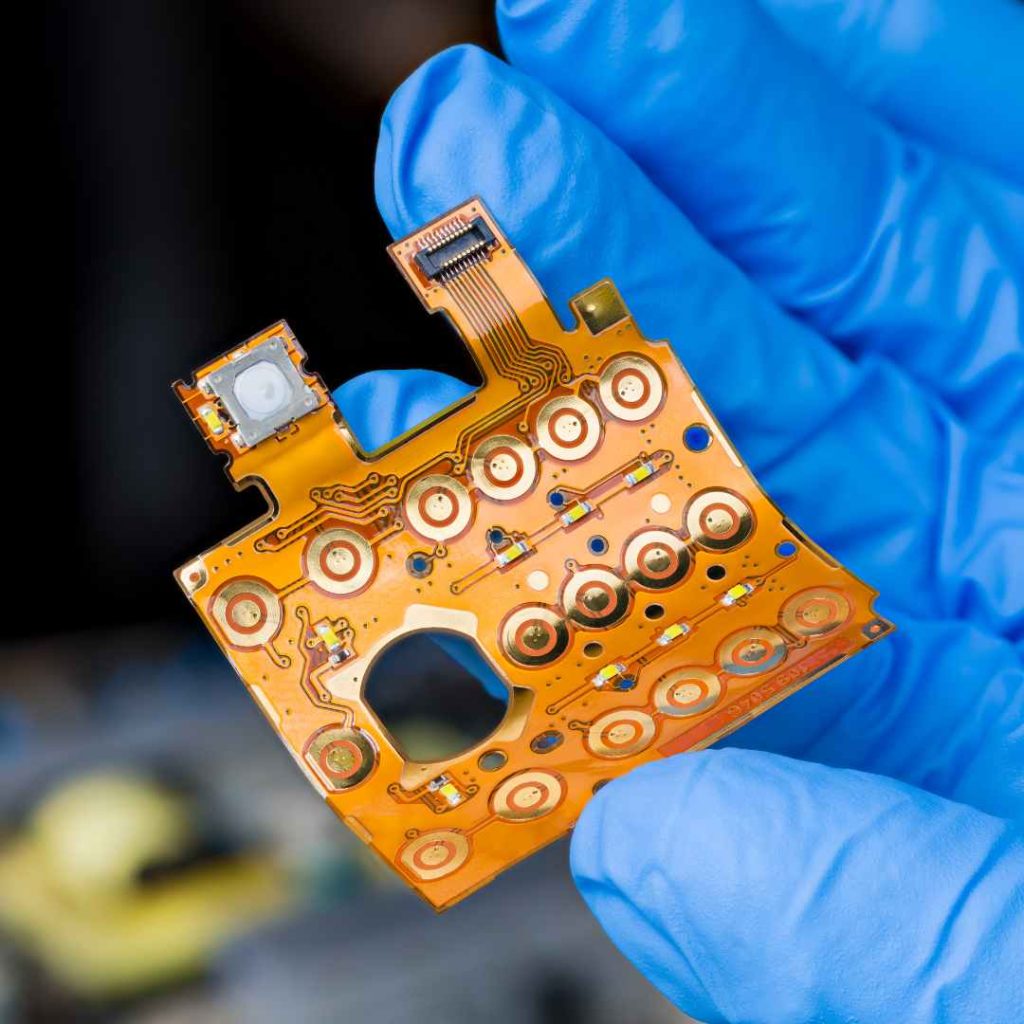
Rigid-Flex PCBs: As the name suggests, these PCBs combine the benefits of both rigid and flexible circuits. They consist of one or more rigid PCB sections interconnected by flexible sections. The rigid sections provide a stable platform for mounting components, while the flexible sections act as “hinges” or “bridges,” allowing the board to be folded or bent into complex three-dimensional shapes. This hybrid construction offers a unique combination of stability and flexibility.

Advantages of Flexible PCBs
Flexible PCBs offer a range of advantages that make them ideal for wearable and medical applications:
- Flexibility and Bendability: The most obvious advantage is their ability to bend and flex without damage. This allows for the creation of devices that can conform to the human body, fit into tight spaces, or withstand repeated motion.
- Space and Weight Savings: Flexible circuits are significantly thinner and lighter than traditional rigid PCBs. This is critical for wearable devices where size and weight are paramount.
- Durability and Reliability: High-quality flexible PCBs are surprisingly durable. They can withstand repeated flexing, vibration, and shock, making them suitable for demanding environments.
- Improved Signal Integrity (in some cases): The consistent dielectric properties of the flexible substrate can, in certain high-speed applications, offer advantages in signal integrity compared to traditional rigid boards with multiple layers and vias.
Advantages of Rigid-Flex PCBs
Rigid-flex PCBs build upon the advantages of flexible circuits, adding further benefits:
Combination of Flexibility and Rigidity: The rigid sections provide a solid base for mounting components that require a stable platform (e.g., connectors, BGAs), while the flexible sections allow for bending and folding.
Reduced Assembly Complexity: Rigid-flex PCBs can eliminate the need for connectors between multiple rigid boards, simplifying the assembly process and reducing the overall component count. This also leads to cost savings.
Improved Reliability: By eliminating connectors, rigid-flex PCBs reduce the number of potential points of failure, leading to higher overall system reliability.
Space and Weight Savings: While not as dramatic as purely flexible circuits, rigid-flex PCBs still offer significant space and weight savings compared to multi-board assemblies using rigid PCBs and connectors.

Applications in Wearable Technology
Wearable devices are a prime example of the transformative power of flexible and rigid-flex PCBs. Consider these applications:
- Smartwatches and Fitness Trackers: The curved shape and compact size of these devices are often enabled by flexible circuits that wrap around the wrist.
- Health Monitoring Devices: Flexible sensors that conform to the body can continuously monitor vital signs, providing valuable data for healthcare professionals.
- Smart Clothing: Flexible circuits can be integrated into fabrics, enabling the creation of clothing with embedded sensors, displays, and communication capabilities.
- Augmented Reality (AR) and Virtual Reality (VR) Headsets: Flexible and rigid-flex PCBs are enabling lighter, more comfortable, and more powerful AR/VR headsets.
Applications in Medical Devices
The medical field is also experiencing a revolution thanks to flexible and rigid-flex PCBs:
- Implantable Devices: Pacemakers, cochlear implants, and other implantable devices benefit from the miniaturization and biocompatibility offered by flexible circuits.
- Diagnostic Tools: Endoscopes and other minimally invasive diagnostic tools often utilize flexible circuits to navigate tight spaces within the body.
- Minimally Invasive Surgical Instruments: Flexible circuits can be integrated into surgical instruments, providing surgeons with enhanced control and precision.
- Lab-on-a-Chip Devices: Flexible substrates are being used to create microfluidic devices for rapid diagnostics and point-of-care testing.
Design and Manufacturing Considerations

Designing and manufacturing flexible and rigid-flex PCBs presents unique challenges compared to traditional rigid boards. Careful consideration must be given to:
- Material Selection: Choosing the right substrate material (polyimide, polyester, etc.) and adhesive is crucial for performance and reliability.
- Layer Stackup: The arrangement of rigid and flexible layers in a rigid-flex PCB must be carefully planned to ensure proper functionality and manufacturability.
- Routing: Trace routing on flexible sections requires special attention to avoid stress concentrations and potential cracking.
- Component Placement: Component placement should be optimized for both the rigid and flexible sections, considering factors like bending radius and stress.
BENCOR’s Capabilities
BENCOR offers comprehensive design, fabrication, and assembly services for flexible and rigid-flex PCBs. We have invested in state-of-the-art equipment and developed proven processes to meet the demanding requirements of these technologies. Our capabilities include:
- Expert Design Support: Our experienced engineers can assist you with every stage of the design process, from material selection to layer stackup and routing.
- Advanced Manufacturing Technologies: We utilize cutting-edge equipment and processes to ensure the highest quality and precision in flexible and rigid-flex PCB fabrication.
- Rigorous Testing and Inspection: We implement comprehensive testing and inspection procedures to guarantee the reliability and performance of our products.
- Wide Range of Materials: We provide flex and rigid-flex circuits using a wide array of materials.
Contact BENCOR today to discuss your flexible or rigid-flex PCB project and discover how we can help you bring your innovative wearable or medical device to life.
Conclusion
Flexible and rigid-flex PCBs are no longer niche technologies; they are becoming essential building blocks for the next generation of electronic devices. Their unique combination of flexibility, durability, and miniaturization capabilities is driving innovation in wearable technology, medical devices, and beyond. As these technologies continue to evolve, partnering with an experienced and capable manufacturer like BENCOR is crucial for ensuring the success of your projects. We are committed to providing cutting-edge flexible and rigid-flex PCB solutions that meet the ever-increasing demands of the electronics industry.