Printed circuit board (PCB) assembly is a crucial aspect of medical device development that often goes unnoticed by patients and even many healthcare professionals. However, the quality and reliability of PCB design and assembly can literally mean the difference between life and death when it comes to critical medical equipment. Let’s explore why PCB assembly is so important for medical devices and how it impacts modern medicine.
Medical Device Development and PCBs
The field of medical technology has advanced rapidly in recent decades, with increasingly sophisticated diagnostic and treatment devices relying on complex electronic systems. From MRI machines to portible cardiac defibrillators, printed circuit boards form the backbone of these life-saving technologies.
During the medical device development process, electrical engineers work closely with mechanical engineers and software developers to create PCB designs that meet the exacting standards required for medical applications. Key considerations include:
- Miniaturization: Many medical devices need to be as small and lightweight as possible, especially implantable or wearable technologies. This requires densely packed multilayer PCB designs.
- Reliability: Medical devices often need to function flawlessly for years or even decades. PCB assembly must be extremely high quality to ensure long-term reliability.
- Safety: Any failures in medical device PCBs could put patients at risk. Designs must incorporate redundancies and fail-safes.
- Regulatory Compliance: Medical devices must meet stringent FDA and international regulations, which impacts allowable PCB materials and design elements.
Printed circuit board (PCB) assembly is a crucial aspect of medical device development that often goes unnoticed by patients and even many healthcare professionals. However, the quality and reliability of PCB design and assembly can literally mean the difference between life and death when it comes to critical medical equipment. Let’s explore why PCB assembly is so important for medical devices and how it impacts modern medicine.
Medical Device Development and PCBs
The field of medical technology has advanced rapidly in recent decades, with increasingly sophisticated diagnostic and treatment devices relying on complex electronic systems. From MRI machines to portible cardiac defibrillators, printed circuit boards form the backbone of these life-saving technologies.
During the medical device development process, electrical engineers work closely with mechanical engineers and software developers to create PCB designs that meet the exacting standards required for medical applications. Key considerations include:
- Miniaturization: Many medical devices need to be as small and lightweight as possible, especially implantable or wearable technologies. This requires densely packed multilayer PCB designs.
- Reliability: Medical devices often need to function flawlessly for years or even decades. PCB assembly must be extremely high quality to ensure long-term reliability.
- Safety: Any failures in medical device PCBs could put patients at risk. Designs must incorporate redundancies and fail-safes.
- Regulatory Compliance: Medical devices must meet stringent FDA and international regulations, which impacts allowable PCB materials and design elements.
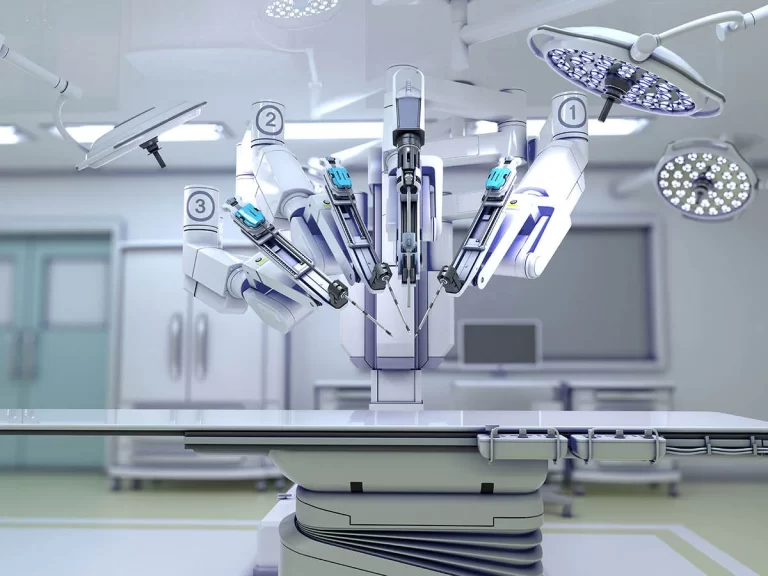
PCB Design Tips for Medical Devices
Designing PCBs for medical applications requires special considerations:
- Use of medical-grade materials: PCB substrate materials and components must meet biocompatibility standards for medical use.
- EMI/RFI shielding: Medical devices are often sensitive to electromagnetic interference, requiring careful PCB layout and shielding techniques.
- Thermal management: Many medical devices generate significant heat, necessitating thermal vias and other cooling strategies in the PCB design.
- Design for manufacturability (DFM): PCB designs should account for the assembly process to ensure high yield and reliability.
- Incorporate test points: Sufficient test points should be included to allow thorough functional testing of the assembled PCB.
- Consider sterilization requirements: PCBs in medical devices may need to withstand autoclave or chemical sterilization processes.
Electronics PCB Assembly for Medical Applications
The PCB assembly process for medical devices involves several critical steps:
- Design verification: Before assembly begins, the PCB design undergoes rigorous testing and simulation to identify any potential issues.
- Component sourcing: Only the highest quality electronic components from vetted suppliers are used to ensure reliability and traceability.
- Precise assembly: State-of-the-art pick-and-place machines and reflow ovens are used to accurately position and solder components.
- Inspection: Automated optical inspection (AOI) and X-ray inspection verify correct assembly and solder joint quality.
- Functional testing: Assembled PCBs undergo extensive electrical testing to verify proper functionality.
- Conformal coating: Many medical device PCBs receive a protective conformal coating to guard against moisture, dust, and chemicals.
- Documentation: Detailed records are kept for the entire assembly process for regulatory compliance and quality assurance.
Electronics PCB Assembly for Medical Applications
The PCB assembly process for medical devices involves several critical steps:
- Design verification: Before assembly begins, the PCB design undergoes rigorous testing and simulation to identify any potential issues.
- Component sourcing: Only the highest quality electronic components from vetted suppliers are used to ensure reliability and traceability.
- Precise assembly: State-of-the-art pick-and-place machines and reflow ovens are used to accurately position and solder components.
- Inspection: Automated optical inspection (AOI) and X-ray inspection verify correct assembly and solder joint quality.
- Functional testing: Assembled PCBs undergo extensive electrical testing to verify proper functionality.
- Conformal coating: Many medical device PCBs receive a protective conformal coating to guard against moisture, dust, and chemicals.
- Documentation: Detailed records are kept for the entire assembly process for regulatory compliance and quality assurance.
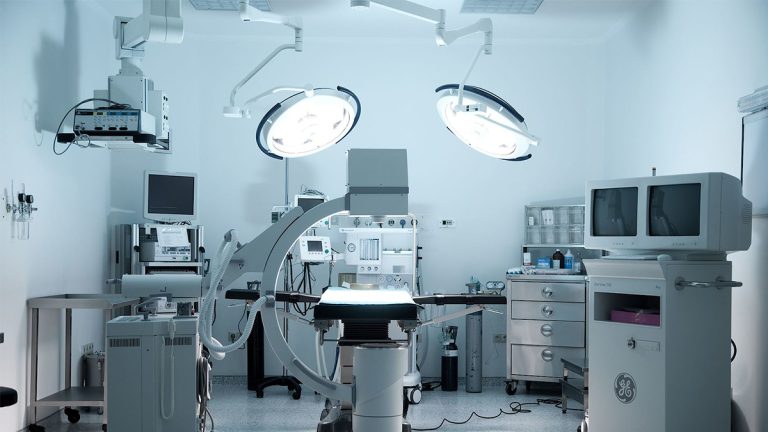
Prototyping and Testing PCB Components
Rigorous prototyping and testing are essential steps in medical device PCB development:
1. Initial prototyping: Early PCB prototypes allow designers to verify form, fit, and basic functionality.
2. Environmental testing: Prototypes undergo temperature cycling, humidity exposure, and vibration testing to simulate real-world conditions.
3. EMC testing: Electromagnetic compatibility (EMC) testing ensures the device won’t interfere with other equipment or be susceptible to external interference.
4. Reliability testing: Accelerated life testing helps predict long-term reliability and identify potential failure modes.
5. Clinical testing: Once a final PCB design is approved, it’s incorporated into fully functional medical device prototypes for clinical trials.
Impact on Modern Medicine
The importance of high-quality PCB assembly in medical devices cannot be overstated. It enables:
- More accurate diagnostics: Advanced imaging and laboratory equipment rely on precise PCB-based control systems.
- Improved patient monitoring: PCBs in telemetry systems and wearable devices allow for continuous monitoring of vital signs.
- Minimally invasive treatments: Tiny PCBs power surgical robots and endoscopic tools for less invasive procedures.
- Personalized medicine: Smart implants and drug delivery systems use PCBs to tailor treatments to individual patients.
- Enhanced accessibility: PCB miniaturization has made home medical devices more portable and affordable.
Medical Device Development and PCBs
The field of medical technology has advanced rapidly in recent decades, with increasingly sophisticated diagnostic and treatment devices relying on complex electronic systems. From MRI machines to portible cardiac defibrillators, printed circuit boards form the backbone of these life-saving technologies.
During the medical device development process, electrical engineers work closely with mechanical engineers and software developers to create PCB designs that meet the exacting standards required for medical applications. Key considerations include:
- Miniaturization: Many medical devices need to be as small and lightweight as possible, especially implantable or wearable technologies. This requires densely packed multilayer PCB designs.
- Reliability: Medical devices often need to function flawlessly for years or even decades. PCB assembly must be extremely high quality to ensure long-term reliability.
- Safety: Any failures in medical device PCBs could put patients at risk. Designs must incorporate redundancies and fail-safes.
- Regulatory Compliance: Medical devices must meet stringent FDA and international regulations, which impacts allowable PCB materials and design elements.
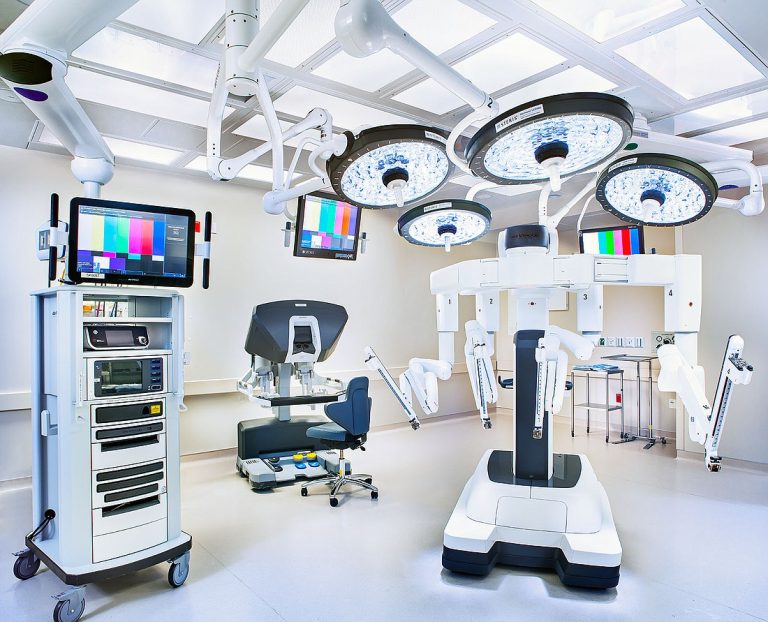
Conclusion
As medical technology continues to evolve, the role of PCB assembly in medical device development will only grow in importance. From the initial design phase through prototyping, testing, and final production, every step of the PCB assembly process is critical to creating safe, reliable, and effective medical devices.
The next time you encounter a piece of medical equipment – whether it’s a simple digital thermometer or an ultrasound station – take a moment to appreciate the intricate printed circuit boards inside that make modern medicine possible. The unseen work of PCB designers and assembly technicians plays a vital role in saving lives and improving patient outcomes around the world.
BENCOR is your trusted partner in the world of non-invasive medical healthcare device manufacturing. With our state-of-the-art printed circuit board assembly (PCBA), production, and component box build services, we stand at the forefront of ensuring that your innovative medical devices meet the highest standards of reliability and performance.