In today’s electronics-driven world, the reliability of Printed Circuit Boards (PCBs) is paramount. From consumer electronics to critical medical devices and aerospace systems, the failure of a PCB can have serious consequences. Therefore, thorough testing and inspection throughout the manufacturing process are essential to ensure that PCBs meet the required specifications and will perform reliably in the field. This rigorous quality control is not just a “nice-to-have” – it’s a fundamental requirement for any reputable PCB manufacturer.
Why is PCB Testing and Inspection So Critical?
PCB manufacturing is a complex process involving numerous steps, each with the potential for defects. Even a small flaw, such as a hairline crack in a trace or a microscopic void in a solder joint, can lead to malfunction or failure of the entire device. Testing and inspection serve to:
Detect Defects Early: Identifying defects early in the manufacturing process is crucial to minimize scrap and rework costs. The earlier a defect is caught, the less expensive it is to correct.
Ensure Compliance with Specifications: Testing verifies that the PCB meets the design specifications, including electrical performance, dimensional accuracy, and material properties.
Prevent Field Failures: Thorough testing reduces the risk of PCBs failing in the field, which can lead to costly repairs, product recalls, and damage to a company’s reputation.
Improve Product Quality: A robust testing and inspection program ultimately leads to higher-quality products and increased customer satisfaction.
Maintain Process Control: Testing data can be used to monitor and improve the manufacturing process, preventing future defects.
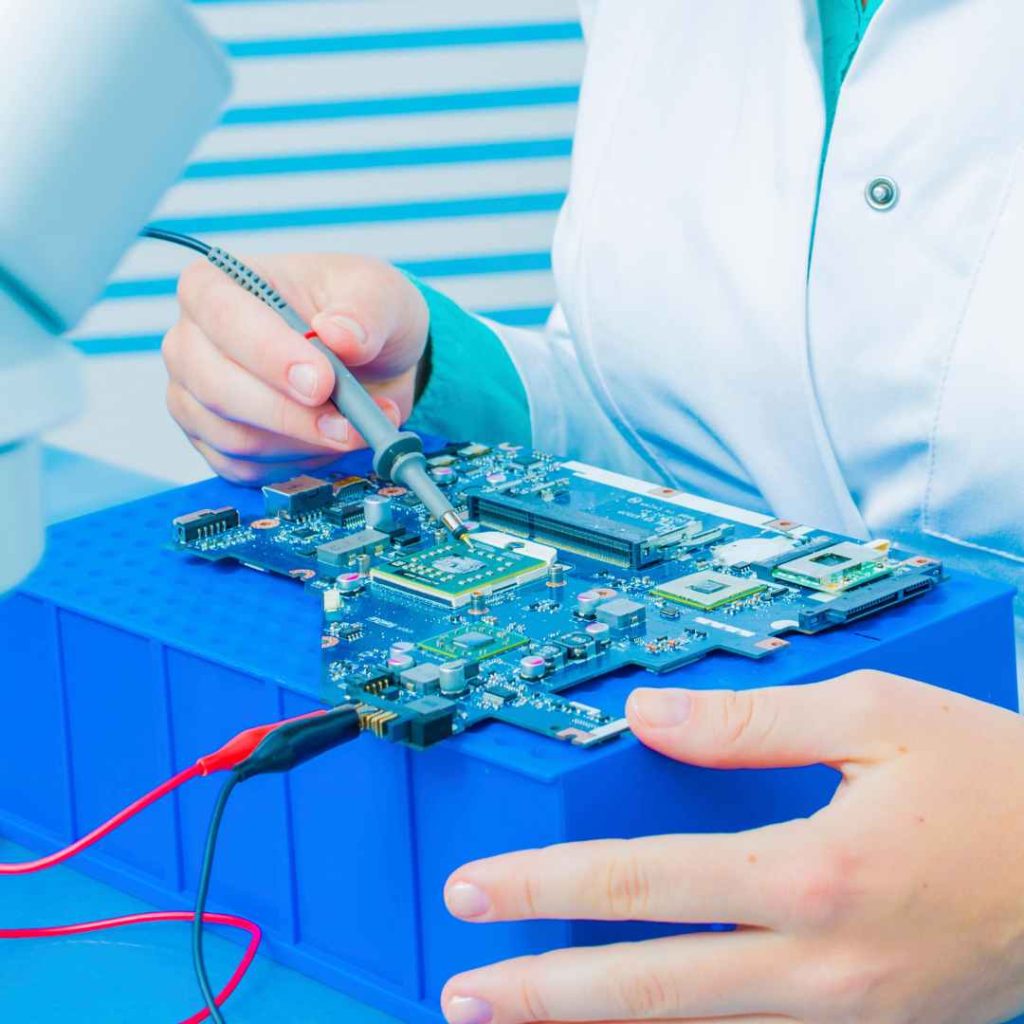
Types of PCB Testing and Inspection
A comprehensive testing and inspection strategy typically involves a combination of different methods, each with its own strengths and limitations. Here are some of the most common techniques:
- Visual Inspection: This is the most basic form of inspection, involving a visual examination of the PCB for obvious defects, such as scratches, contamination, or misaligned components. While it can detect gross errors, it’s limited in its ability to find subtle flaws.
- PTFE (Polytetrafluoroethylene): Also known as Teflon, PTFE offers extremely low dielectric loss and excellent high-frequency performance. It’s often used in microwave circuits and other demanding applications.
- Hydrocarbon-based Laminates: These materials offer a good balance of performance and cost, with lower dielectric loss than FR-4 and good thermal stability.
- LCP (Liquid Crystal Polymer): LCP offers excellent dimensional stability, low moisture absorption, and good high-frequency performance.
- Automated Optical Inspection (AOI): AOI uses high-resolution cameras and sophisticated image processing software to automatically inspect PCBs for a wide range of defects, including missing components, incorrect component placement, solder bridges, and open circuits. AOI is much faster and more consistent than manual visual inspection.
- X-ray Inspection: X-ray inspection allows for the non-destructive examination of the internal structure of a PCB. It’s particularly useful for detecting hidden defects, such as voids in solder joints, internal layer misregistration, and problems with Ball Grid Array (BGA) components.
- In-Circuit Testing (ICT): ICT uses a “bed of nails” fixture to make electrical contact with specific test points on the PCB. It can measure the values of individual components and verify the functionality of circuits. ICT is effective for detecting shorts, opens, and incorrect component values.
- Flying Probe Testing: Flying probe testing uses robotic probes to make contact with test points on the PCB. It’s more flexible than ICT, as it doesn’t require a dedicated fixture for each board type. It’s often used for prototype testing and low-volume production.
- Functional Testing: Functional testing verifies the overall operation of the PCB by simulating its intended use. This typically involves connecting the PCB to a test system that provides inputs and monitors outputs. Functional testing is the most comprehensive form of testing, but it can also be the most time-consuming and expensive.
- Burn-In Testing: The purpose of burn-in testing is to detect early failures, also known as infant mortality, in a population of PCBs.



BENCOR’s Commitment to Quality and Reliability
BENCOR understands the critical importance of testing and inspection in PCB manufacturing. They implement rigorous quality control procedures throughout their entire process, from design to final assembly. BENCOR’s commitment to quality includes:
ISO 9001:2015 Certification: BENCOR’s quality management system is certified to ISO 9001:2015, demonstrating their commitment to consistent quality and continuous improvement.
Advanced Inspection Equipment: BENCOR utilizes state-of-the-art equipment for AOI, X-ray inspection, and electrical testing.
Experienced Personnel: BENCOR’s team of engineers and technicians are highly trained in inspection and testing procedures.
Detailed Documentation: BENCOR maintains thorough documentation of all testing and inspection results.
Customized Testing Solutions: BENCOR can develop customized testing plans to meet the specific requirements of each customer and application.
Continuous Improvement: BENCOR is constantly evaluating and improving its testing and inspection processes to ensure the highest levels of quality and reliability.

The Future of PCB Testing and Inspection
As PCB technology continues to evolve, with increasing complexity and miniaturization, the demands on testing and inspection will also increase. We can expect to see greater use of automation, artificial intelligence (AI), and machine learning to improve the speed, accuracy, and efficiency of testing.
BENCOR is committed to staying at the forefront of PCB testing and inspection technology and to providing its customers with the assurance that their PCBs will meet the highest standards of quality and reliability. Contact BENCOR today to discuss your testing and inspection needs and learn how they can help you ensure the success of your products. They will find the best solution for your needs.