In the intricate world of modern electronics, where devices are relentlessly pushed to be more powerful, more compact, and more efficient, effective thermal management stands as a silent guardian. As processing speeds increase and component densities rise, the heat generated within electronic enclosures can become a significant threat to performance, reliability, and the overall lifespan of the product. While passive cooling techniques play their part, active cooling, primarily driven by fans, is often essential to maintain optimal operating temperatures.
The two predominant types of fans employed in these critical roles are axial fans and centrifugal fans. Understanding their distinct characteristics, operational principles, and, crucially, the best practices for integrating them into an enclosure design is paramount for any engineer or designer. At BENCOR, as a dedicated American manufacturer of complex electronic systems, we recognize that proficient thermal design and meticulous assembly of these cooling components are integral to delivering the high-quality, reliable products our nation’s industries depend on.

The Unseen Guardian: Why Effective Airflow is Crucial in Electronic Systems

The necessity for robust cooling in electronic systems cannot be overstated. Every active component, from microprocessors and FPGAs to power transistors and voltage regulators, generates heat as a byproduct of its operation. If this heat is not effectively dissipated, component temperatures can rise beyond their specified limits. This excess heat doesn’t just make a device warm to the touch; it directly impacts sensitive semiconductor junctions, accelerating material degradation, altering electrical characteristics, and significantly shortening the component’s operational life.
The primary mechanism for removing this heat from within an enclosure is convection, and fans are the workhorses that drive forced convection. They create a continuous stream of cooler ambient air flowing over hot components, absorbing thermal energy and then expelling the heated air out of the enclosure. Without this active intervention, heat would build up, leading to a cascade of negative consequences.
Inadequate thermal management can manifest in various ways, all detrimental to the end product. Performance throttling, where a processor intentionally slows itself down to avoid overheating, is a common symptom. System instability, random resets, or unexpected shutdowns can frustrate users and lead to data corruption. Over the long term, consistently high operating temperatures drastically reduce the Mean Time Between Failures (MTBF) of components, leading to premature product failure, increased warranty claims, and damage to brand reputation. In extreme cases, overheating can even pose safety hazards.
Understanding Axial Fans: The High-Volume Air Movers
Axial fans are perhaps the most recognizable type of fan, commonly seen in personal computers and various electronic equipment.
How Axial Fans Operate
The design of an axial fan is relatively straightforward. It features propeller-like blades that are mounted to a central hub, which in turn is connected to a motor shaft. As the blades rotate, they draw air in and accelerate it in a direction that is parallel to the motor shaft – hence the term “axial.” Think of it like an airplane propeller; it moves air straight through itself.
Key Characteristics of Axial Fans
The defining characteristic of axial fans is their ability to move a high volume of air, typically measured in Cubic Feet per Minute (CFM) or Cubic Meters per Minute (CMM). They achieve this high flow rate efficiently when there is minimal resistance to the airflow. However, they generally produce lower static pressure compared to centrifugal fans of a similar size. This means they are less effective at pushing air through dense obstacles or restrictive pathways. Axial fans are often available in compact, square, or round frames, making them relatively easy to integrate into various enclosure designs.
Common Applications in Electronic Enclosures
Given their characteristics, axial fans are widely used for general case cooling in devices like desktop PCs, servers, and consumer electronics, where the primary goal is to exchange a large volume of air within the enclosure. They are also effective for providing ventilation in power supplies, spot cooling individual components that have open access to airflow, and in any application where the system impedance (resistance to airflow) is relatively low.

Demystifying Centrifugal Fans: The High-Pressure Specialists
Centrifugal fans, also commonly referred to as radial fans or simply blowers, operate on a different principle and are designed for different challenges.
How Centrifugal Fans Operate
A centrifugal fan features an impeller, which is essentially a wheel with a series of blades, housed within a specially shaped casing (often resembling a snail shell or squirrel cage). Air is drawn into the center of the rotating impeller axially (parallel to the shaft) and is then accelerated outwards by the centrifugal force generated by the rotating blades. This air is then collected by the housing and expelled at a 90-degree angle from the intake, typically through a specific outlet duct or port.
Key Characteristics of Centrifugal Fans
The primary advantage of centrifugal fans is their ability to generate significantly higher static pressure than axial fans. This makes them highly effective at overcoming resistance to airflow, such as that created by densely packed components, heatsinks with high fin density, air filters, or long and convoluted ductwork. While they excel at pressure, their overall airflow volume for a given size might be less than that of a comparable axial fan. They can also be somewhat noisier due to the air turbulence created within the housing.
Common Applications in Electronic Enclosures
Centrifugal fans are the preferred choice in systems with high impedance to airflow. This includes densely packed server racks where air must be forced through multiple layers of components, applications requiring air to be pushed through high-efficiency particulate air (HEPA) filters, or systems where air must be ducted precisely to cool specific hot spots. They are also commonly found in laptops and other compact portable devices where directed, high-pressure airflow is needed to cool components in confined spaces.

Axial vs. Centrifugal Fans: A Head-to-Head Comparison
To crystallize the differences, consider this summary:
- Airflow Direction: Axial fans move air parallel to their shaft; Centrifugal fans expel air perpendicular (90 degrees) to their shaft.
- Static Pressure vs. Airflow Volume: Axial fans generally offer high airflow volume at low static pressure; Centrifugal fans deliver high static pressure, often with a more moderate airflow volume.
- Typical Noise Profile: For a similar airflow, axial fans tend to be quieter, though specific design and operating speed heavily influence noise. Centrifugal fans can be noisier due to higher pressures and turbulence.
- Size and Form Factor Considerations: Axial fans are often slimmer and available in standard square/round frames. Centrifugal fans typically have bulkier housings due to the impeller and volute design.
- Ideal Use Cases Summarized: Axials for general ventilation and low-impedance systems; Centrifugals for high-impedance systems, ducted applications, and focused cooling.
Strategic Integration: Design Considerations for Fans in Enclosures
Selecting the correct fan type is only half the battle; its effective integration within the electronic enclosure is equally critical for achieving optimal thermal performance. Poor integration can negate the benefits of even the most powerful fan.
Fan Placement and Crafting an Effective Airflow Path
Strategic positioning of fans is paramount. The goal is to create a clear, unobstructed path for cool ambient air to enter the enclosure, flow over the heat-generating components, and for the heated air to be efficiently exhausted. This involves careful consideration of intake and exhaust vent locations. Designers often aim for a positive pressure setup (more intake than exhaust to keep dust out) or a negative pressure setup (more exhaust than intake to draw air through specific paths). It’s crucial to avoid “dead spots” where hot air can stagnate or situations where hot exhaust air is immediately drawn back into an intake (short-circuiting).
Understanding and Managing System Impedance
System impedance refers to the total resistance the airflow encounters as it moves through the enclosure. This resistance is created by everything in the airflow path: component density, PCB layout, heat sinks, cables, filters, and the design of intake/exhaust grilles. A high system impedance requires a fan capable of generating high static pressure (typically a centrifugal fan) to maintain adequate airflow. Attempting to use a low-pressure axial fan in a high-impedance system will result in significantly reduced airflow and poor cooling.
Noise Reduction Strategies in Fan Integration
Acoustic noise is a significant consideration in many electronic products, particularly consumer devices and office equipment. Fan selection plays a role – choosing fans with lower decibel (dBA) ratings, better bearing types (e.g., fluid dynamic bearings over sleeve bearings), and optimized blade designs can help. Proper mounting is also key; using vibration-dampening grommets or mounts can prevent fan vibrations from transferring to the chassis and amplifying noise. Implementing fan speed control, often via Pulse Width Modulation (PWM), allows the fan to run slower (and quieter) when thermal loads are low, ramping up only when necessary.
Filtration for Longevity and Performance
In environments prone to dust, dirt, or other airborne particulates, incorporating air filters at the fan intakes is essential. Filters prevent these contaminants from accumulating on PCBs and heat sinks, which can act as an insulating blanket, impede airflow, and potentially cause short circuits or corrosion. The enclosure design must allow for easy access to these filters for regular cleaning or replacement to maintain their effectiveness.
Power Delivery and Cable Management
Fans require a stable power source, typically provided via connectors on the PCB or a dedicated system power supply. The design must ensure that fan power cables are properly routed and secured to prevent them from obstructing airflow, getting caught in fan blades, or creating electromagnetic interference (EMI). BENCOR’s expertise in custom cable assembly and meticulous PCB assembly ensures these connections are robust and neatly managed.
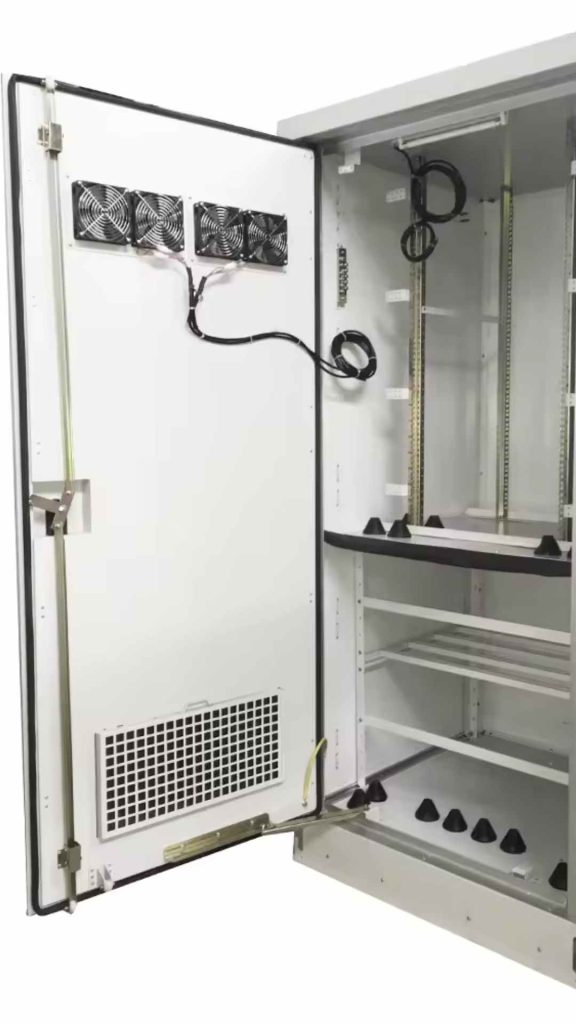
The Bigger Picture: System-Level Thermal Design and BENCOR's Role
Effective fan selection and integration are vital components of a comprehensive, system-level thermal management strategy. The design of the PCB itself plays a significant complementary role. Strategic placement of high-power components to align with primary airflow paths, the use of ample copper planes within the PCB layers for heat spreading, and the judicious application of dedicated heat sinks on critical components all work in concert with active fan cooling.
For complex systems, engineers increasingly rely on thermal simulation tools (Computational Fluid Dynamics – CFD) during the design phase. These tools can model airflow patterns, predict temperature distributions, and help optimize fan placement and heat sink design before physical prototypes are even built, saving significant time and cost.
While BENCOR may not manufacture the fans themselves, our role as a premier American electronics manufacturer is crucial in bringing these thermally optimized designs to life. Our precision in PCB design review (DFM/DFA), high-quality PCB fabrication and assembly, and meticulous execution of complex box build assemblies ensure that all components – including critical cooling systems like fans, heat sinks, and thermal interface materials – are integrated exactly as specified by the engineering design. This unwavering commitment to quality assembly, performed right here in our Texas facility, is fundamental to achieving the intended thermal performance and overall reliability of the sophisticated electronic systems our customers entrust to us.
Conclusion:
Choosing between an axial and a centrifugal fan, and then strategically integrating it into an electronic enclosure, is a critical engineering decision that directly influences product reliability, performance, and lifespan. Axial fans offer high volume for general cooling, while centrifugal fans provide the high pressure needed for more restrictive environments. However, the fan itself is only part of the equation; intelligent enclosure design, careful consideration of system impedance, and attention to detail in assembly are all paramount. Robust thermal management is not an afterthought but a cornerstone of dependable, high-performance electronics. By partnering with an experienced, quality-focused US-based electronics manufacturer like BENCOR, you ensure that these critical thermal design considerations are expertly implemented during every stage of the assembly process, leading to products that operate coolly, reliably, and proudly bear the mark of American manufacturing excellence. Ensure your electronic systems perform at their best; contact BENCOR for expert assembly of your thermally optimized designs.