In the competitive world of electronics manufacturing, time-to-market and cost-effectiveness are paramount. Getting a product from concept to production quickly and efficiently, while maintaining high quality, is a significant challenge. Design for Manufacturing (DFM) and Design for Assembly (DFA) are two crucial methodologies that address this challenge, focusing on optimizing the design of a Printed Circuit Board (PCB) for ease of manufacturing and assembly.
What is Design for Manufacturing (DFM)?
DFM is the process of designing a PCB with the manufacturing process in mind. It involves making design choices that simplify fabrication, reduce the likelihood of defects, and minimize manufacturing costs. DFM considerations include:
- PCB Material Selection: Choosing the appropriate PCB material (FR-4, high-frequency laminates, etc.) based on the application requirements and manufacturability.
- Layer Stackup: Optimizing the arrangement of copper layers and dielectric materials to achieve the desired electrical performance and minimize manufacturing complexity.
- Trace Width and Spacing: Ensuring that trace widths and spacing meet the capabilities of the manufacturing process and the requirements for signal integrity.
- Via Design: Selecting appropriate via types (through-hole, blind, buried, microvias) and optimizing their size and placement to ensure reliable connections and manufacturability.
- Solder Mask Design: Ensuring that the solder mask openings are properly sized and positioned to prevent solder bridging and other defects.
- Silkscreen Design: Creating clear and legible silkscreen markings to aid in component placement and identification.
- Panel Design: Optimizing the arrangement of multiple PCBs on a panel to maximize material utilization and minimize waste.
- Component Selection: Choosing readily available and cost-effective components.
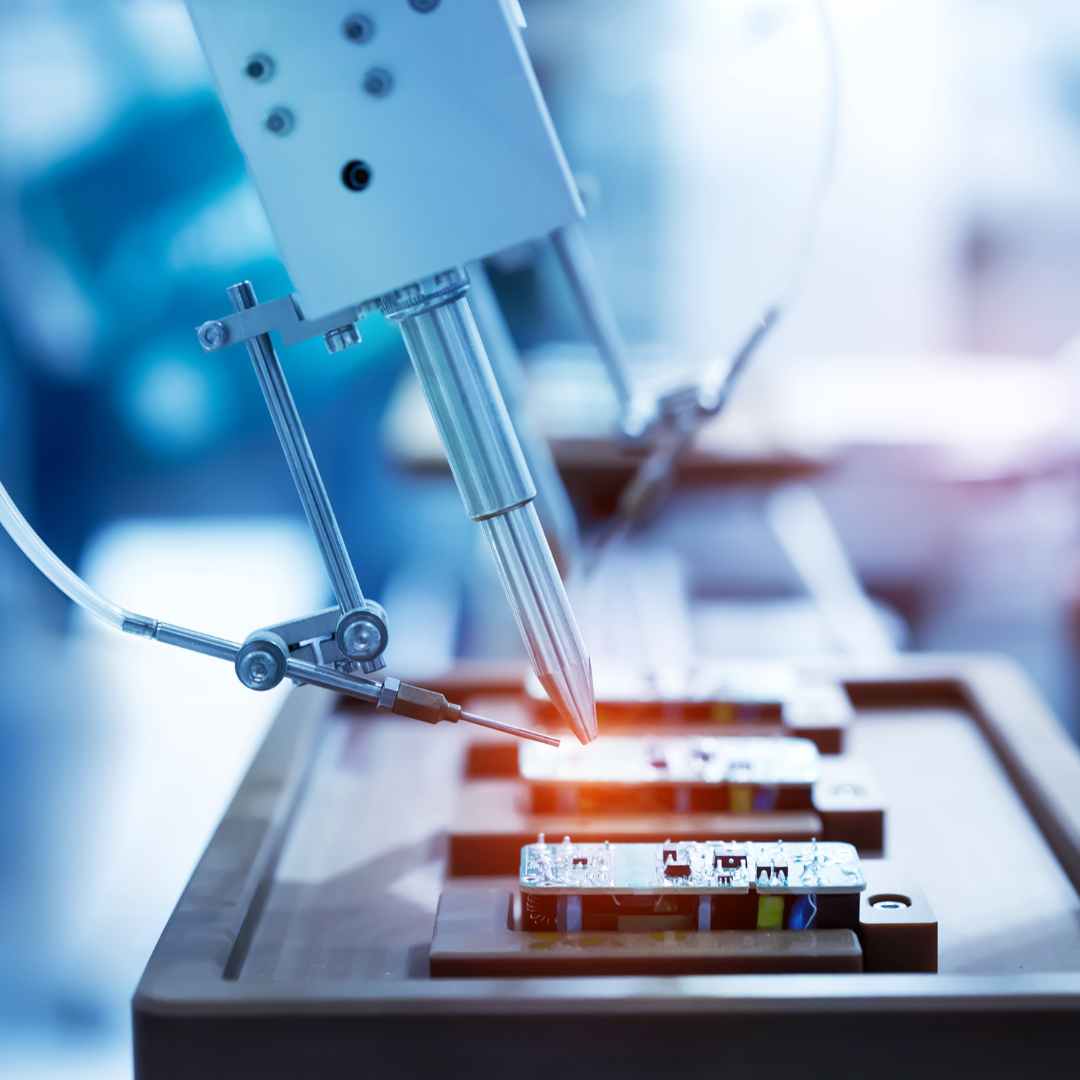


What is Design for Assembly (DFA)?
DFA focuses on designing a PCB for ease of assembly, whether it’s manual assembly or automated assembly using pick-and-place machines. DFA principles include:
Component Orientation: Orienting components in a consistent manner to simplify automated placement.
Component Spacing: Providing adequate spacing between components to allow for easy placement, soldering, and inspection.
Component Selection: Choosing components that are compatible with automated assembly equipment.
Test Point Placement: Including strategically placed test points to facilitate in-circuit testing (ICT) and functional testing.
Fiducial Marks: Adding fiducial marks (reference points) to the PCB to enable accurate component placement by automated equipment.
Clearance for Tooling: Ensuring adequate clearance around components for tooling used in the assembly process, such as soldering irons and pick-and-place nozzles.
Minimizing Component Variety: Reducing the number of different component types to simplify the assembly process and reduce inventory costs.
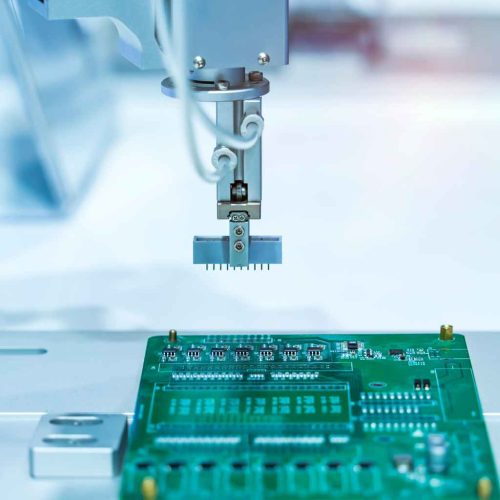
Benefits of DFM and DFA
Implementing DFM and DFA principles offers numerous benefits:
- Reduced Manufacturing Costs: By simplifying the manufacturing and assembly processes, DFM and DFA can significantly reduce costs.
- Improved Product Quality: DFM and DFA minimize the likelihood of defects, leading to higher-quality products.
- Faster Time-to-Market: By streamlining the manufacturing process, DFM and DFA can accelerate product development cycles.
- Increased Reliability: Well-designed PCBs are less prone to failure, resulting in more reliable products.
- Reduced Rework and Scrap: DFM and DFA minimize the need for rework and reduce scrap rates, saving time and money.
- Improved Yields: DFM and DFA lead to higher manufacturing yields, meaning more usable PCBs from each production run.
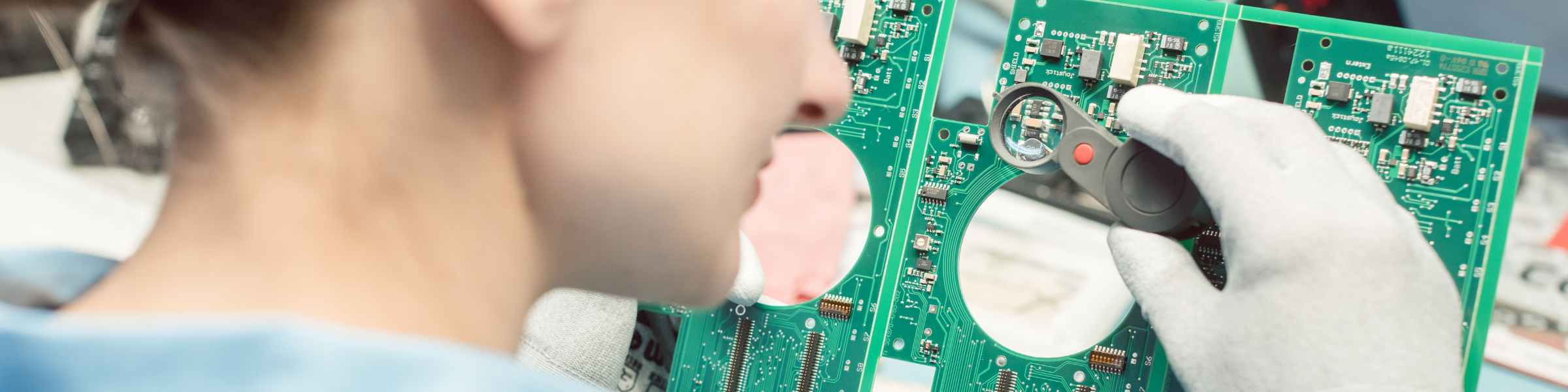
BENCOR’s Expertise in DFM/DFA
BENCOR understands the critical importance of DFM and DFA in achieving efficient and cost-effective PCB production. They offer their expertise of their engineering team to assist clients:

Early Design Collaboration: BENCOR’s engineers work closely with customers early in the design process to provide DFM/DFA guidance.
Design Reviews: BENCOR conducts thorough design reviews to identify potential manufacturing and assembly issues before production begins.
Recommendations for Improvement: BENCOR provides specific recommendations for design modifications to optimize manufacturability and assembly.
Experience with a Wide Range of Technologies: BENCOR has experience with various PCB technologies, including high-density interconnect (HDI), microvias, and advanced materials, allowing them to provide tailored DFM/DFA solutions.
Turn-Key solutions: Bencor provides turnkey solutions, from the PCB design to the assembly, making the customer’s job easier.
The Future of DFM/DFA
As electronic devices become more complex and miniaturized, the importance of DFM and DFA will only continue to grow. Advanced software tools, incorporating artificial intelligence (AI) and machine learning, are being developed to automate and optimize DFM/DFA processes.
BENCOR is committed to staying at the forefront of DFM/DFA best practices and to providing its customers with the expertise they need to achieve efficient and cost-effective PCB production. Contact BENCOR today to discuss your project and learn how their DFM/DFA services can help you optimize your designs and streamline your manufacturing process. Their team will be able to provide all the answers.