For decades, the electronics industry has operated on a largely linear model: take resources, make a product, and encourage the consumer to dispose of it and buy a new one when it becomes obsolete or fails. This “take-make-dispose” paradigm fueled incredible innovation and growth, but it has come at a steep environmental cost. We are now facing a global electronic waste (e-waste) crisis, with millions of tons of valuable and often hazardous materials being discarded in landfills each year. In response to this challenge, a more intelligent and sustainable model is gaining critical momentum: the Circular Economy. The goal of a circular economy is to move away from disposability and instead create systems where products are kept in use for as long as possible, and their components and materials are recovered, repaired, and reintegrated at the end of their life. A foundational, practical principle for achieving this is Designing for Disassembly (DfD). It is a conscious, upfront design philosophy focused on creating products that can be easily and economically taken apart. As a responsible American manufacturer, BENCOR believes that supporting these forward-thinking principles is not just good for the planet—it’s essential for the future of innovative and resilient manufacturing.
The End of the Linear Model: Why We Must Rethink Electronics Design
The linear model’s unsustainability is now undeniable. The sheer volume of e-waste is staggering; it is the fastest-growing domestic waste stream globally. Each discarded device represents a significant loss of valuable resources. Precious metals like gold, palladium, silver, and copper, along with rare earth elements vital for modern technology, are thrown away at an alarming rate. At the same time, these discarded products can leach hazardous materials like lead, mercury, and cadmium into the soil and groundwater, posing serious environmental and health risks.
Beyond the environmental toll, the economic case for change is compelling. It is simply unsustainable to continue mining finite resources only to entomb them in landfills after a single use. This recognition, coupled with a growing global “Right to Repair” movement and increasingly stringent environmental regulations, particularly in Europe, is putting immense pressure on manufacturers to evolve. The future does not belong to disposable technology; it belongs to products designed for longevity, serviceability, and circularity.

Core Principles of Designing for Disassembly (DfD)
Designing for Disassembly is not an abstract concept; it is a set of practical, actionable strategies that engineers and designers can implement today. These principles focus on making end-of-life processing, whether for repair, refurbishment, or recycling, as efficient and straightforward as possible.
Use of Standardized, Non-Proprietary Fasteners
One of the biggest obstacles to repair and disassembly is the use of strong adhesives and proprietary fasteners that require specialized, often unavailable, tools. The DfD approach champions the use of standard, common fasteners like Phillips or Torx screws. This simple choice makes a product significantly more accessible for both professional technicians and end-users, facilitating repairs and the separation of components for recycling. It’s a move away from sealed black boxes towards open, serviceable hardware.
Embracing Modular Design and Component Accessibility
A modular design architecture is a cornerstone of DfD. This involves designing the product with distinct, easily replaceable sub-assemblies. For example, the power supply board, the main logic board, and the I/O interface board could all be separate modules connected by standard cables or connectors. If one module fails, it can be swapped out without having to discard the entire device. Furthermore, components that are most likely to fail or require replacement, such as batteries, charging ports, and mechanical switches, should be designed to be easily accessible without requiring the disassembly of the entire product.
Minimizing Adhesives and Welded Components
Glues and strong adhesives are the enemies of disassembly and recycling. A smartphone screen glued firmly to its chassis, for instance, makes replacement incredibly difficult and risky. At the recycling stage, it prevents the clean separation of the glass from the metal frame, often contaminating both material streams. DfD encourages the use of mechanical alternatives like clips, gaskets, and screws, which allow for the non-destructive separation of parts.
Clear Labeling of Materials for Efficient Recycling
For materials to be effectively recycled, they must be properly sorted. A key DfD principle is to clearly mark all significant plastic and metal parts with standard material identification codes (e.g., >ABS<, >PC<, >ALU<). This simple step allows recycling facilities to quickly and accurately sort materials, dramatically increasing their value and the likelihood that they will be reclaimed and used in new products rather than being sent to a landfill.
Designing for a Safe and Logical Separation Sequence
A well-designed product has a logical, intuitive disassembly sequence. Engineers should consider the order of operations for taking the product apart, ensuring it is safe and efficient. This includes making sure that high-voltage components like capacitors are discharged or protected, and that volatile components like lithium-ion batteries can be removed early and safely without risk of puncture.
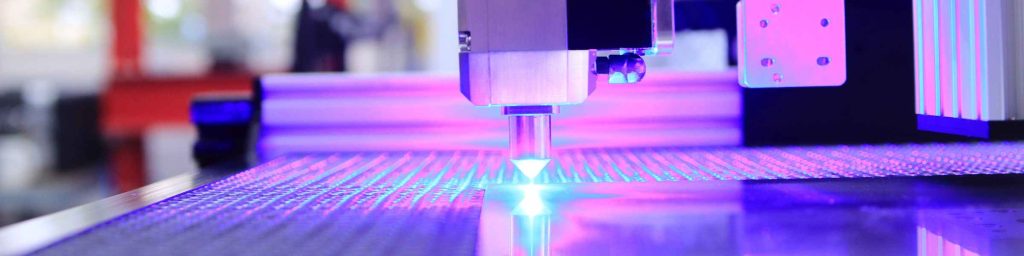
The BENCOR Advantage: A Partner in Responsible Manufacturing
While BENCOR does not typically design the end-product’s mechanical enclosure, we are a critical partner in its realization and a strong supporter of these forward-thinking principles. Our role as an assembler of complex systems positions us perfectly to help bring modular, serviceable products to life.
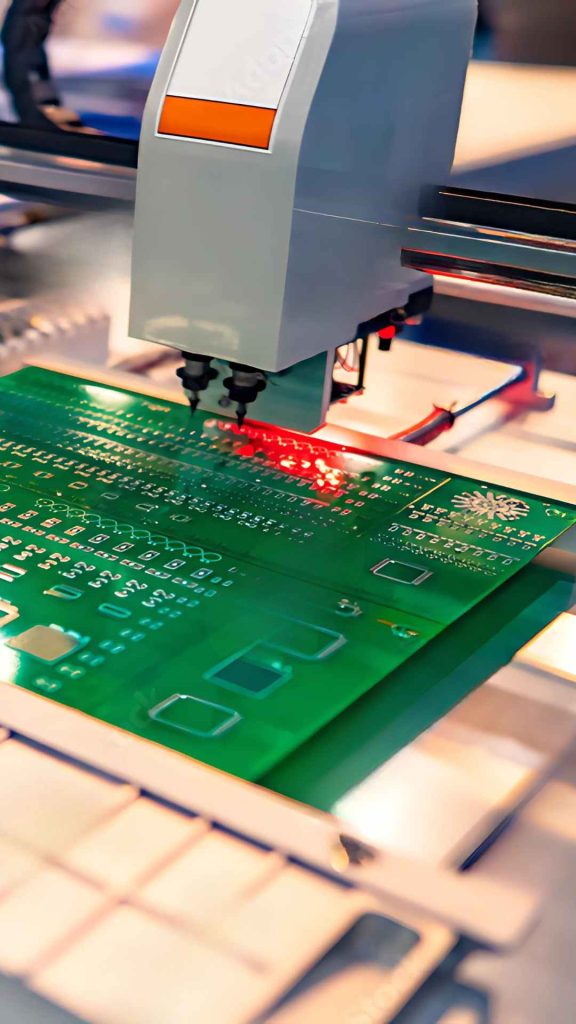
Expertise in Modular and System-Level Assembly
BENCOR’s extensive experience with complex box build assemblies makes us an ideal partner for products designed with modularity in mind. We understand how to efficiently manage the integration of multiple sub-assemblies, intricate cable harnesses, and mechanical components into a final, cohesive system, ensuring the designer’s intent for a modular architecture is perfectly executed.
A Foundation of High-Quality, Reliable Connections
For a product designed to be repaired and have a long life, the initial build quality must be exceptional. A product designed for circularity cannot be built with subpar connections that are doomed to fail. BENCOR’s unwavering commitment to quality ensures that every solder joint, every crimped wire, and every connector we install is robust and reliable, providing the durable foundation that a long-lifecycle product requires.
A Commitment to American Responsibility
The shift towards a circular economy and responsible manufacturing is a hallmark of industrial leadership and ingenuity. We believe that embracing these principles is a reflection of the best of American manufacturing – a focus not just on initial production, but on creating durable, high-value products that last. As a US-based manufacturer, BENCOR is a transparent and accountable partner in this ecosystem, committed to the long-term value and environmental stewardship that benefits our customers, our community, and our country.
The Business Case for Designing for Disassembly
Embracing DfD is not just an act of environmental goodwill; it is an increasingly smart business strategy with tangible benefits.
Enhanced Brand Reputation and Customer Loyalty
In an era of conscious consumerism, companies that are demonstrably sustainable and that support their customers’ right to repair often gain significant brand loyalty and a powerful positive reputation.
Creation of New Revenue Streams
A serviceable product design opens the door to new revenue streams. Companies can profit from selling genuine spare parts, offering authorized repair services, or creating a business around refurbishing and reselling returned units.
Future-Proofing Against Regulations
By proactively designing products for disassembly and repair, companies can stay ahead of the curve, preparing themselves for the inevitable strengthening of “Right to Repair” laws and other environmental legislation, thus avoiding costly, reactive redesigns in the future.
Reduced Lifecycle Costs
Products that are easier to take apart are also cheaper to service under warranty. Furthermore, efficient disassembly can lower the costs associated with responsible end-of-life processing and material recovery.
Conclusion:
The traditional linear “take-make-dispose” model for electronics is fundamentally broken, and the future belongs to the circular economy. Designing for Disassembly is not merely a trend but a powerful, practical, and necessary principle for creating the next generation of sustainable electronic products. It requires a new way of thinking for designers, a commitment to longevity over disposability, and a close, collaborative partnership with a quality-focused manufacturing partner who can expertly assemble these thoughtful, serviceable systems. BENCOR is proud to be that American partner, ready to help build the durable, repairable, and responsible products that will define a more sustainable future.